deep hole gun drilling machines were originally used for gun barrels (commonly known as deep hole barrels, which are not made of seamless precision tubes, and the precision tube manufacturing process cannot meet the accuracy requirements at all.) This is why the manufacturing industry is named gun drills. With the continuous development of technology and the unremitting efforts of manufacturers of deep hole machining systems, deep hole machining has become a convenient and efficient machining method. It is widely used in fields such as the automotive industry, aerospace industry, structural construction industry, medical equipment industry, mold/tool/fixture industry, as well as oil pressure and air compression industry.
Gun drill is an ideal solution for deep hole processing. The use of gun drill can achieve precise machining results, resulting in precise hole positions, high straightness, coaxiality, and high surface finish and repeatability. It can conveniently process various forms of deep holes, and can also solve special deep holes, such as cross holes, blind holes, and flat bottom blind holes.
deep hole gun drilling machines
1. It belongs to the special deep hole machining tool for external chip removal. The V-shaped angle is 120 °.
2. Special machine tools for gun drilling are used.
3. The cooling and chip removal method is a high-pressure oil cooling system.
4. There are two types of cutting heads: ordinary hard alloy and coated.
Deep hole drilling: 1. It belongs to the special deep hole machining tool for external chip removal. The V-shaped angle is 160 °.
2. Dedicated to deep hole drilling systems.
3. The cooling and chip removal method is pulse high-pressure spray cooling.
4. There are two types of cutting heads: ordinary hard alloy and coated.
Gun drill is an effective tool for deep hole machining, with a wide range of machining ranges, from mold steel, fiberglass, Teflon and other plastics to high-strength alloys such as P20 and chromium nickel iron alloy for deep hole machining. In deep hole machining with strict tolerance and surface roughness requirements, gun drills can ensure the dimensional accuracy, positional accuracy, and straightness of the holes.
To achieve satisfactory results when processing deep holes with a gun drill, it is necessary to proficiently master the performance of the gun drill system (including tools, machine tools, fixtures, accessories, workpieces, control units, coolant, and operating procedures). The technical level of the operator is also important. According to the structure of the workpiece and the hardness of the workpiece material, as well as the working conditions and quality requirements of the deep hole machining machine, selecting appropriate cutting speed, feed rate, tool geometric parameters, hard alloy grade, and coolant parameters can achieve excellent machining performance.
Standard deep hole gun drilling machines can process holes with apertures ranging from 1.5mm to 76.2mm, with drilling depths up to 100 times the diameter. The specially customized gun drill can process deep holes with an aperture of 152.4mm and a depth of 5080mm.
Due to the fact that the cutting head is made of hard alloy, the cutting speed of gun drills is much higher than that of high-speed steel drills. This can increase the feed rate of the gun drill per minute. In addition, when using high-pressure coolant, its chips can be effectively discharged from the processed hole, without the need for regular tool retraction during the drilling process to discharge the chips.
Dezhou btadrilltools Not only does it stay in the manufacturing of deep hole machining machines, but the production and deep hole machining business of deep hole drills are also the largest professional manufacturers in Germany.
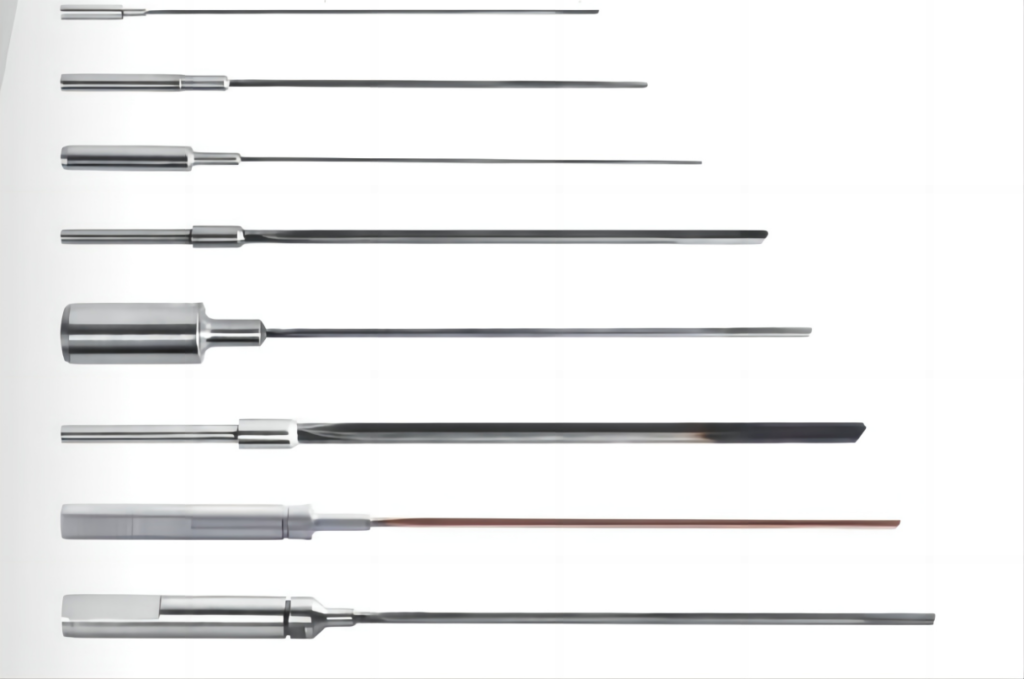
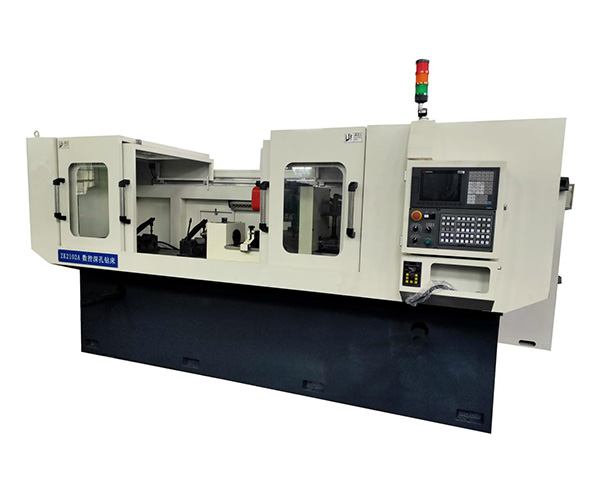