The process of professional deep hole drilling can be roughly divided into the following steps:
1. During the process of entering the guide hole, the deep hole drill does not have any support, and the spindle speed needs to be controlled within a certain range. If the speed is too high, the tool will be broken under centrifugal force.
2. The deep hole drill enters the guide hole, and during this process, the deep hole drill has not actually cut yet. However, under the drive of the spindle, the tool will move in the radial direction. Even if the spindle speed is low at this time, the tool will inevitably rub against the guide hole wall, so the tool needs to be fed low during this process. When the deep hole drill moves to a distance of about 1 mm from the bottom of the guide hole with constant processing parameters, the machine tool opens the cutting fluid circulation (providing cooling, lubrication, and chip removal for subsequent processing).
3. The next step in the process, usually to save time and optimize the processing program, is to use deep hole drilling with low feed and low speed processing to 2-3 times the diameter depth, which increases the spindle speed and tool feed without taking any measures. This process has drawbacks, such as φ The performance of tools below 5 is significant, and the sudden change in feed during processing has a significant impact on the cutting edge, which can exceed the bearing capacity of the tool itself, leading to blade breakage. This situation is very dangerous, but if the blade breakage is not replaced in a timely manner, there is a risk of tool breakage.
4. Deep holes are usually connected to other holes. When the tool is processed to the penetration position, the force on the cutting edge of the tool changes sharply, manifested in the cutting edge not cutting at the same time, but first and then, so that the first cutting edge loses support, and the balance of support force on both sides is broken. The tool is affected by the cutting force on the other side, causing the drill bit to shift and deviate too much, which is reflected in the tool and the tool will break; This is reflected in changes in the positional accuracy of the workpiece, and the parallelism of the deep hole will exceed the tolerance. This situation is inevitable in machining. To effectively reduce the problems of tool breakage and poor positioning, the spindle speed and feed should be reduced to 1/3 of the original data at a distance of 5 mm from the through position. This can effectively reduce the force imbalance of the tool during cutting, and the positional accuracy and parallelism are also greatly improved.
5. Tool retraction: Due to the processing characteristics of deep hole drilling and the limitations in parallelism, the tool may experience bending deformation in the hole during retraction. Therefore, rapid retraction cannot be used, but the speed and feed can be faster than the feed. The specific parameters can be determined based on the actual processing conditions.
if you still have question to deep hole drilling, you can contact me sales@btadrilltools.com
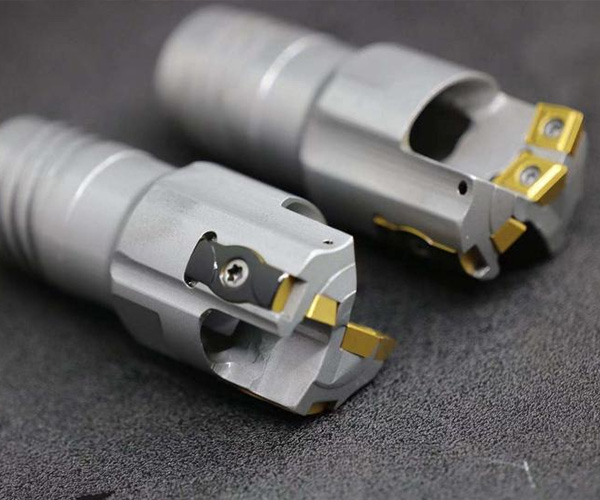
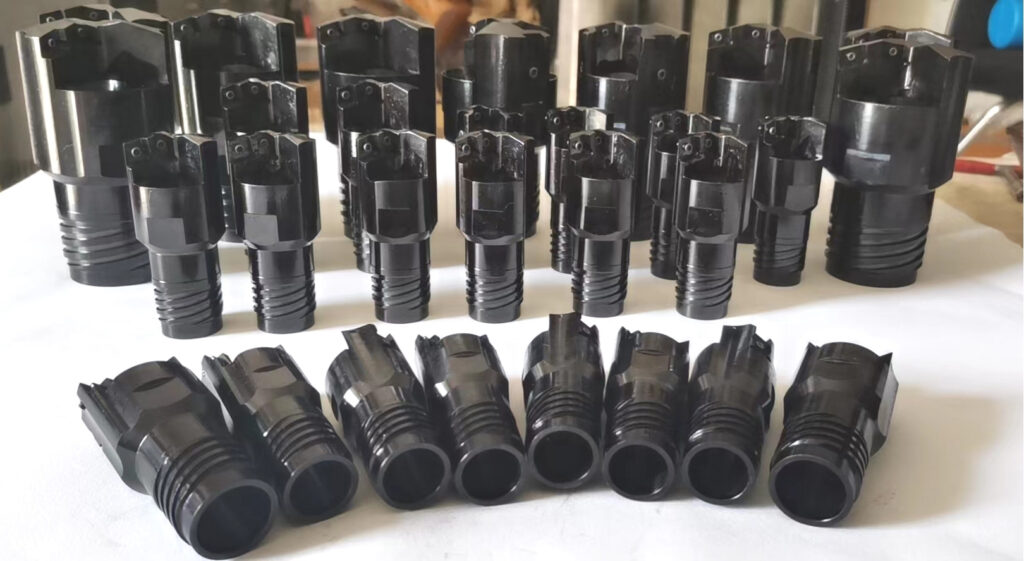