Do you know how to machining stainless steel? Stainless steel machining is a difficult-to-machine material that requires special attention during processing in various industries. Here are some basic requirements for machining stainless steel:
1. Brief Description of Stainless Steel Types and Machinability
Stainless steel is mainly divided into three categories: ferritic stainless steel, austenitic stainless steel, and martensitic stainless steel. These stainless steels have high strength and hardness at high temperatures, large plasticity and toughness, a strong tendency for work hardening, and difficulty in chip separation, curling, and breaking. The friction between the tool and the chip, as well as between the tool and the workpiece, is intense, resulting in high cutting specific energy consumption. Most of the energy is converted into heat, causing the cutting temperature to rise. This leads to the formation of a hardened surface layer in the cutting area. Additionally, the low thermal conductivity of stainless steel results in a small amount of heat being carried away by the chips, leading to more heat being transmitted to the tool, causing the tool temperature to rise and wear to increase. The presence of many fine carbide particles in stainless steel also accelerates tool wear. Stainless steel has a strong affinity for other metal materials, making it prone to the formation of built-up edge during cutting, which makes it difficult to obtain a smooth machined surface.
The machining order of these three types of stainless steel, from easiest to hardest, is ferritic stainless steel > martensitic stainless steel > austenitic stainless steel.
Note: Generally, alloy steels with Cr content greater than 12% or Ni content greater than 8% are referred to as stainless steel. For example, Cr12MoV is known as a die steel, but due to its 12% Cr content, its machinability is similar to that of stainless steel. When selecting parameters and tools, it is necessary to follow the requirements for machining stainless steel to avoid rapid tool wear or tool chipping.
2. Basic Requirements for Stainless Steel Machining
– Select appropriate tools and cutting parameters: Due to the tendency for work hardening and high hardness at high temperatures in stainless steel, it is necessary to use specially designed tools and choose appropriate cutting speeds, feeds, and depths.
– Ensure adequate cooling and lubrication: Due to the high temperatures and wear generated during the cutting process of stainless steel, effective cooling and lubrication agents are required to reduce cutting temperatures and reduce tool wear.
– Control cutting forces: Due to the high strength and toughness of stainless steel, cutting forces are large, so it is necessary to ensure that the machine tool and fixture have sufficient rigidity to control vibrations during the cutting process.
– Maintain tool sharpness: Tool sharpness is crucial for machining stainless steel, as a dull tool increases cutting forces and heat, accelerating tool wear.
– Avoid built-up edge formation: By optimizing cutting parameters and keeping the tool clean, the formation of built-up edge can be reduced, thus achieving better machined surface quality.
In summary, machining stainless steel requires special attention and techniques to ensure machining quality and extend tool life.
to deep hole drilling machining, stainless steel machining is still difficult, if you have some question ,please contact dezhou btadrilltools industrial co.,ltd
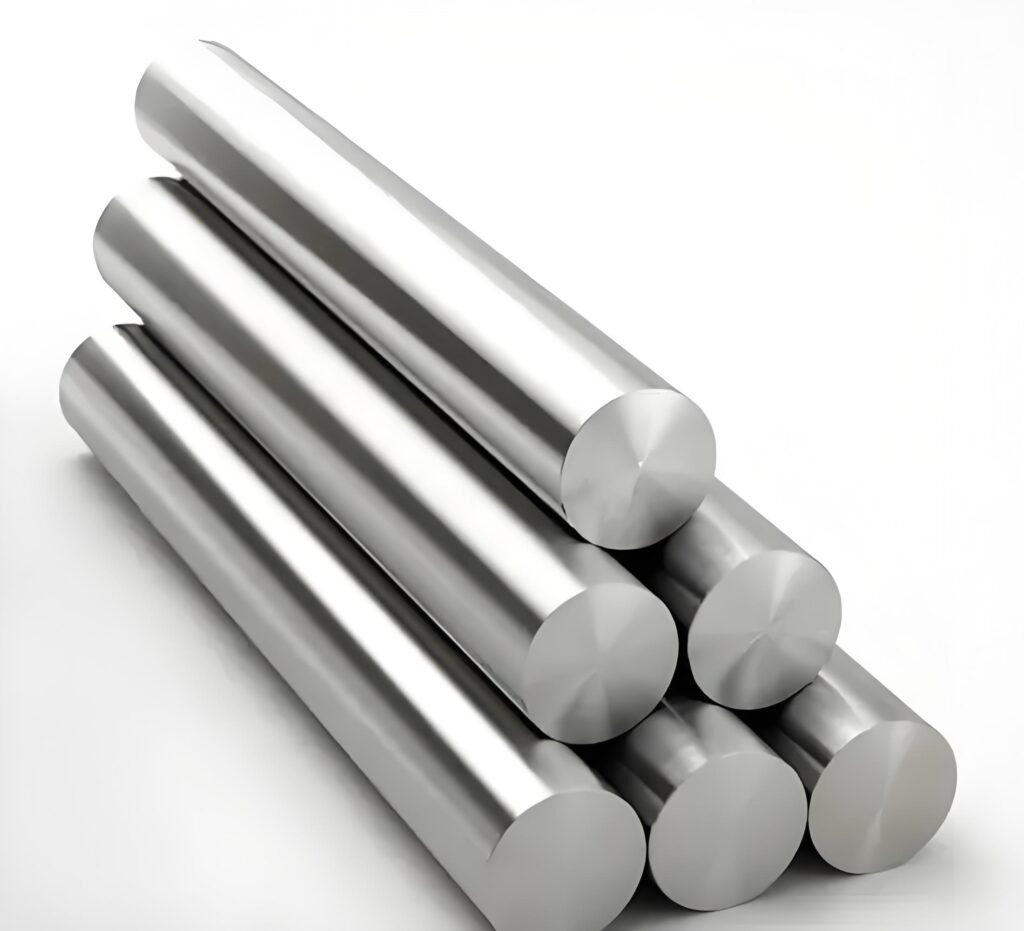
and if you have stainless steel question ,welcome to disucss with our company engineer. sales@btadrilltools.com