may be you are seeking a china deep hole drilling machine or using china deep hole drilling machine .
this article will help you know how to prevent deep hole drilling machine from collision,this experience from Dezhou btadrilltools industrial co.,ltd
three minutes read
As you know,deep hole processing can be divided into three modules: programming, tool setting and automatic processing.
Among them, programming and tool setting are preparatory work for processing operation. Whether the programming is correct, whether the selected cutting parameters are reasonable, and whether the input of tool setting parameters is accurate will be shown in the actual processing. Therefore, in order to ensure the accuracy of NC machine tool processing operations, trial machining is usually required to check whether there are problems in the automatic processing of NC machine tools. In the trial processing, strictly follow the processing principle of “three looks, two needs, and one stop”, which can greatly reduce the collision problem in the machine tool operation.
1.look
1.1 Look at the program.
All operations of CNC deep hole drilling machine tools are controlled by program instructions. Through checking program statements and program names, find out the existing problems and correct them in time. When checking the program, in order to avoid repeated inspection or missing inspection, a certain inspection sequence should be followed: first, from the program name, because the completion of the basic NC operation requires a large number of program instructions to control, so a large number of program files will also be stored in the microcontroller system, and the program name will be automatically lowered, especially the suffix of the program name and the program format should be checked; Second, examine the program fragments. Use the form of computer software simulation to detect whether there are errors in the specific program statements. If there are problems in the upper and lower logic of the statements, the simulation software will automatically point out the existing problems, so that programmers can modify the program in time until there are no problems in the operating program.
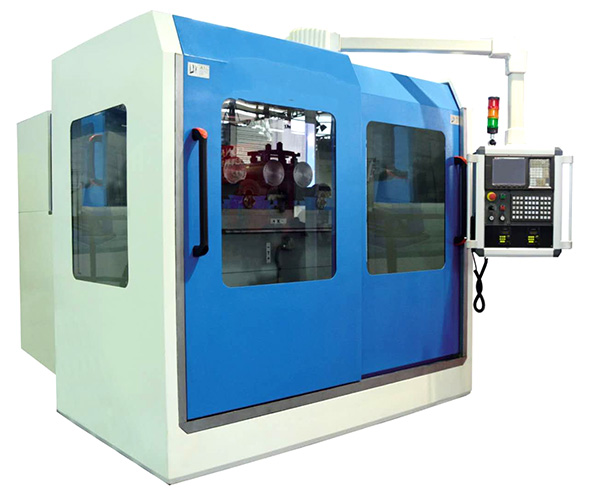
1.2 look at the workpiece coordinates.
The screen will display the machine coordinate, workpiece coordinate and other details of the current tool. When checking, pay attention to comparing the screen value with the actual tool tip position to ensure that the coordinate values between the two can correspond one by one. Due to the influence of such factors as fixture and tool wear, the workpiece coordinates often have certain errors. If the error exceeds the standard range, it will affect the machining progress of the machine tool and cause collision problems. Therefore, this problem can be effectively avoided by comparing the workpiece coordinates.
1.3 look at the position of the tool tip.
The machining and cutting operations of CNC machine tools are completed by tools, so the tool tip position should be checked when checking the machine tools. The tool tip will wear after being used for a period of time. On the premise of not affecting the machining quality of the machine tool, the machine tool operator should regularly adjust the tool position to prevent the tool from colliding with the workpiece or chuck. In addition, the actual position of the tool tip should also be compared with the data displayed on the screen. If there is a large error between the two values, the processing operation should also be stopped. After the shutdown, the tool should be exited and reinstalled and adjusted.
2.Action
2.1 single segment execution.
All CNC deep hole drilling machines have the single section SBL execution function. After starting this function, the processing operation will be automatically terminated when the microcontroller completes a control program. The CNC machine operator needs to manually start the next section of program to carry out processing operations. The advantage of single stage execution is that it gives operators sufficient inspection time, including tool inspection, coordinate inspection and program inspection, so as to greatly avoid collision accidents. Although single segment execution reduces the efficiency of NC machine tool processing, it can greatly improve the processing quality and avoid collision problems. Compared with the overall processing effect, it is better.
2.2 low magnification.
By adjusting the speed adjustment knob of the CNC machine tool to reduce the feed speed of the tool, it is possible to observe whether the tool tip position is consistent with the coordinate display value before the tool is processed. If the two values are different, the equipment can be shut down in time to avoid collision. Especially when machining the inner hole of the workpiece, it is easy to make mistakes in tool feeding or tool withdrawing, which will not only affect the machining quality of the inner hole, resulting in serious deviation of the size of the inner hole of the workpiece, but also lead to the problems of tool binding and tool collision. Therefore, selecting low magnification processing speed can effectively avoid the above processing problems.
3. stop
To be exact, it should be paused several times during automatic processing. By pausing, the operator can have enough mental preparation to observe and compare the position of the tool tip and the display of the screen coordinates. In particular, when the chip is wound onto the workpiece or the tool, the cycle stop key can be pressed. This time can be used to solve the problems in the processing of the NC machine tool and prevent errors due to confusion during the operation.
above is from a china deep hole drilling machine manufacturer suggestion, hope can help you